Notre gamme de robots industriels à grande vitesse, à la pointe de la technologie, comprend des robots à forte capacité, à portée étendue, des robots 7 axes extrêmement agiles, ou encore des robots double bras à 15 axes.
Fully automated machining centres and parts cleaning. Combatting personnel shortages with robots
Yaskawa robots are automating machining centres, including the connected parts cleaning systems, at a leading supplier of products and solutions for sanitary, heating and cooling systems in Landau/Palatinate. The robotics showcase project is the perfect solution for companies suffering from staff shortages, and offers a number of other advantages.
Watts Industries Deutschland GmbH is the German subsidiary of Watts Water Technologies, a global company founded in the United States that generated sales of around two billion US dollars in 2022 with more than 4,500 employees worldwide. More than 170 attractive jobs are located in Landau in der Pfalz. Here the company produces primarily innovative products for water-carrying heating and air conditioning systems.
What stands out during the site visit is the high vertical range of manufacture, and production is correspondingly well equipped. Processing machines of all kinds work in shifts, including several identical machining centres from Alzmetall that perform the machining of pipes of different lengths. These subsequently serve as distribution systems for underfloor heating.
For more than ten years, semi-skilled employees were tasked with the loading and unloading of these machining centres in multiple machine operation. Andreas Becker, Industrial Engineer at Watts Industries, explains why the company urgently needed to invest in the automation of these machines: “Here at the site we are suffering from a massive shortage of personnel. To ensure the continuous operation of the machines in shift operation, the only option was to invest in robots. This step opened up the possibility of qualifying the freed-up employees on the machines for higher-level tasks, relieving them of the daily contact with cooling lubricants that loading and unloading inevitably entails.”
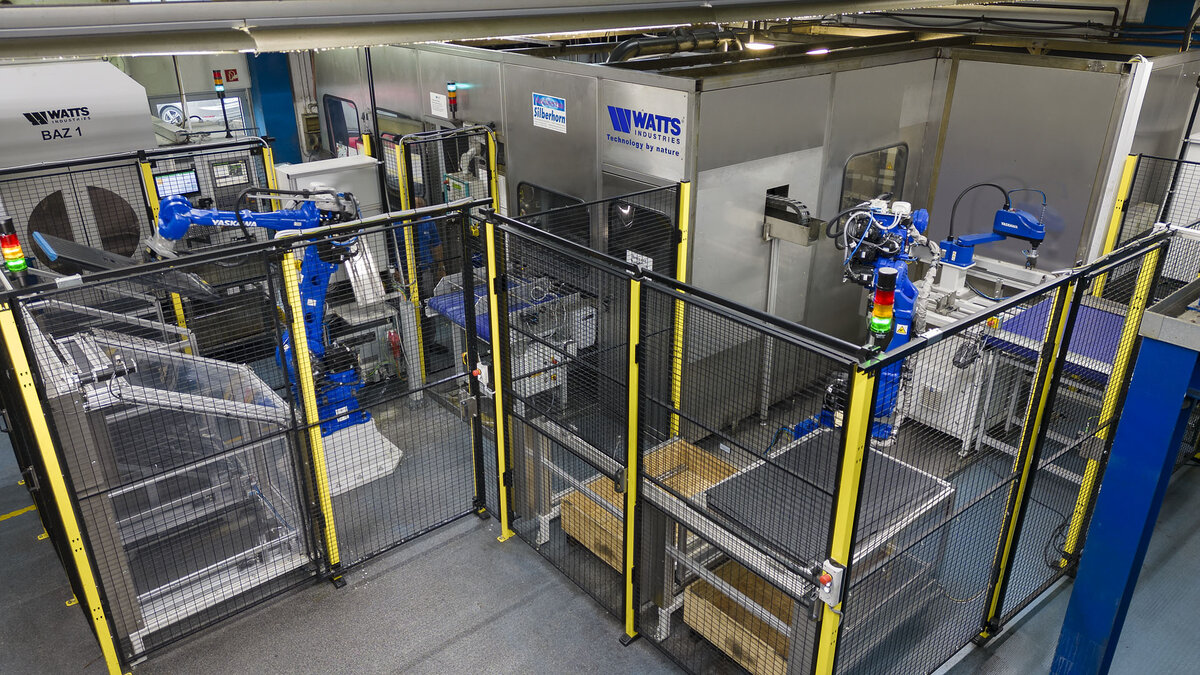
Challenging project fully automated with Yaskawa robots
However, the project to automate the machines and connected parts cleaning system was accompanied by major challenges. Heiko Röhrig, Sales Manager of EGS Automation GmbH, recalls: “The automation of machine tools with Yaskawa robots is standard for us. Things looked different at Watts. Here, not only the severely limited space available in production caused us headaches, but also the provision of the parts with high tolerances in workpiece carrier trolleys.”
These trolleys are welded structures made of sheet metal, which, as they were never intended for automation, may have greater manufacturing tolerances. Up to 15 workpiece carriers with up to 48 parts can be accommodated on a trolley – stacked on top of each other and placed at an angle. The trolleys are manually fed into the system at a defined position and locked into place.
In order to compensate the tolerances of the trolleys for precise robot handling, EGS Automation has come up with a convincing solution: Each Yaskawa six-axle Motoman GP50 is equipped with a sensor on the gripping tool that is resistant to cooling lubricants. With this sensor the robot approaches several defined positions and determines a correction factor for the current coordinate system. The real challenge for the robot starts once the actual stack height, including any tilt, has been determined.
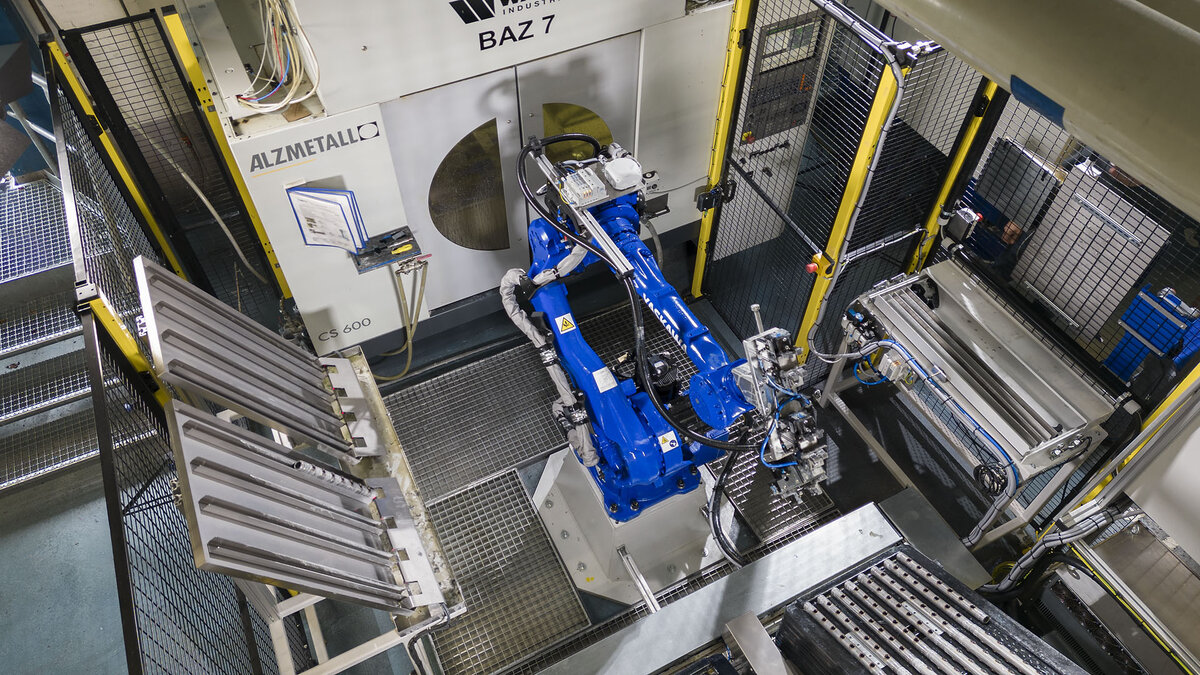
Four pipes in simultaneous machining
As soon as the doors of the machining centre open, every second counts. The large Yaskawa six-axle robot quickly moves into the working area of the machine. With its double gripper it removes two of the four machined pipes and places them on a buffer pallet. There it picks up two raw parts and inserts them into the machine. In the same operation it removes the last machined pair from the machine and loads the second raw part pair. Then it withdraws from the machine, the door closes and the machining of four pipes continues in one clamping process.
Only after loading and unloading does it becomes clear why the Motoman GP50 is equipped with a further single gripper. As Heiko Röhrig explains, “The pipes reach the plant in tightly-packed plastic blisters that do not permit simultaneous removal of two pipes with the double gripper. As there is sufficient time during the runtime of the machine, the GP50 separates the pipes, part by part, on a buffer pallet within reach of the double gripper. From there, the six-axis robot can handle the pipes in pairs, resulting in a significantly reduced loading and unloading time on the machine.”
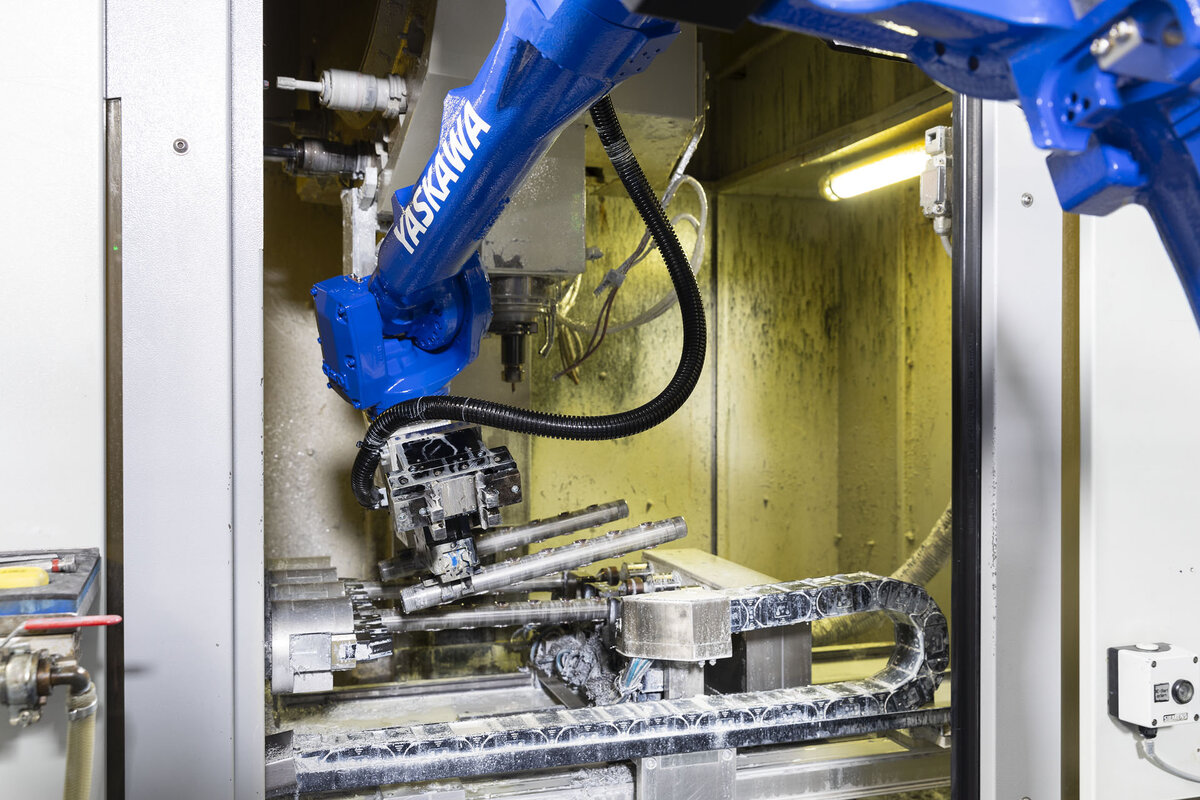
Computational programming instead of teaching variants
Today, pipe blanks in different lengths from 120 mm to 750 mm, with two different diameters and optionally in brass or stainless steel, have already increased the number of variants to over 50. To avoid the greater effort involved in teaching the numerous variants, we rely on a purely mathematical program. The operator must only enter certain parameters such as pipe length, bore spacing, etc., and the program does the rest," says Heiko Röhrig.
Other key goals in automation include maximum autonomy, short set-up times and maximum flexibility. The concept of the system, which works from a blank to a finished part carriage – the Motoman GP50 changes the respective workpiece carriers via a special function of its double gripper – leaves nothing to be desired. The flexibility of the machining centres, in combination with the variability of robot-assisted automation, enables the production of many variants and relatively small batch sizes with unprecedented cost-effectiveness.
Andreas Becker confirms that in the choice of robot Watts relied on the expertise of the plant manufacturer EGS Automation and never regretted it. “The Motoman GP50 from Yaskawa offers enough reserves in terms of load capacity and range, to be prepared for future applications. In addition, its waterproof wrist ensures 100% reliability, even with intensive exposure to cooling lubricants. Furthermore, the sixth axis is so slim that we can also cope very well in the confined space in the working area of the machine.”
Robots automate subsequent parts cleaning
When a workpiece carrier trolley is fully loaded with machined parts, an operator removes it and transports it to the parts cleaning system, which is automated with Yaskawa SG650 and Motoman GP50 four- and six-axis robots. To ensure greater autonomy, a total of three trolley spaces are available, with the robot having access to two places. The third slot is reserved for the operator to change the trolleys, ensuring uninterrupted automatic operation.
In the continuous cleaning system, the dirt side is separated from the clean side. The uncleaned pipes are loaded by a GP50, which places them on a feed belt. After completion of brushing, deburring and cleaning, the parts leave the system on the clean side on a conveyor line.
Here a fast Yaskawa-Scara SG650 takes over the handling of the parts. With maximum dynamics, it inserts the pipes into a station in which they are rotatively aligned using a laser sensor, based on the bores. In the last step, another GP50 picks up the pipes and places them in wooden boxes for onward transport. In order to achieve the highest possible packing density in the boxes, EGS Automation has developed a special gripper that grips the tubes not at the circumference but in their radial bores, and can thus place them close to each other.
In conclusion, the overriding goals associated with automation were fully realized, including some immunity to the shortage of personnel, higher productivity, improved self-sufficiency and, last but not least, the creation of a clean working environment for employees without skin contact with cooling lubricants.
Andreas Becker is also enthusiastic about something else: The project management of EGS Automation proved to be extremely reliable. Time and cost calculations were meticulously adhered to, even under the adverse conditions of the Covid pandemic. The Yaskawa robots proved to be equally reliable; they quickly became valued colleagues among the workforce, as they are very easy to operate and take on unpopular tasks.”
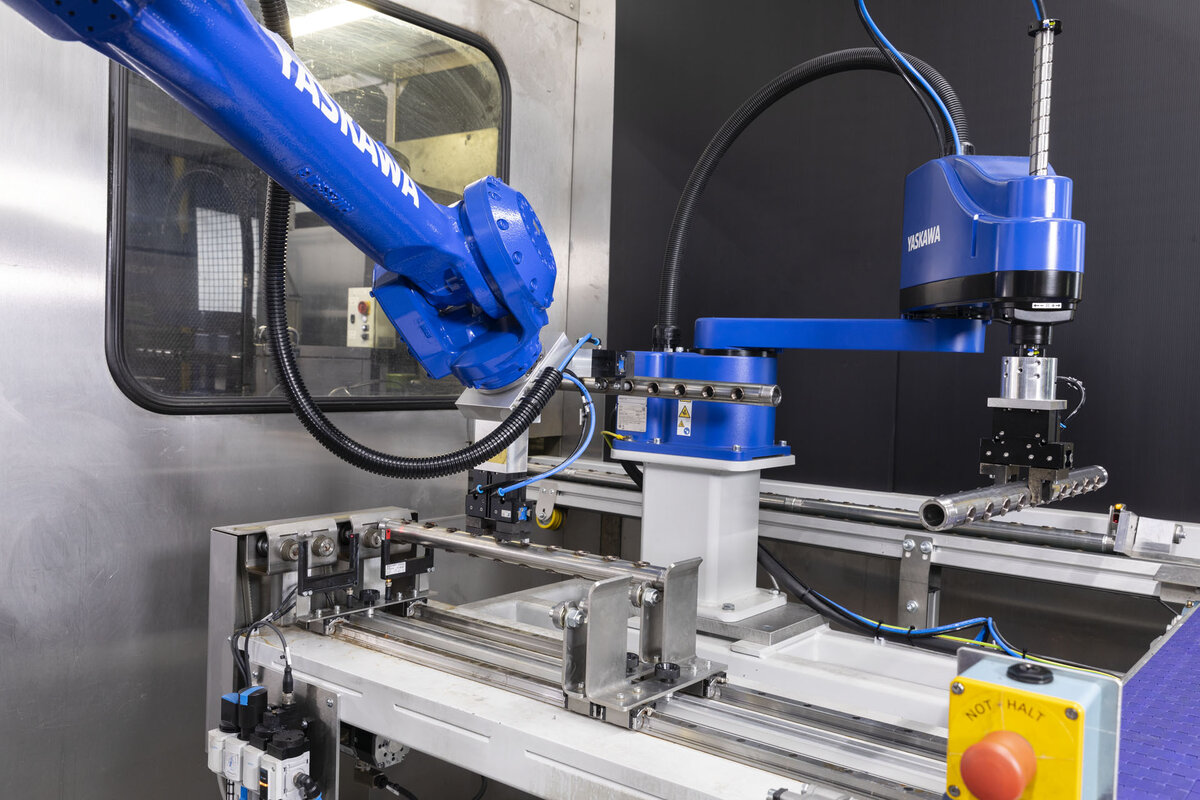
Text: Ralf Högel
Contact for readers’ enquiries:
Yaskawa Europe GmbH
Tel. +49-8166-90-0
robotics@yaskawa.eu
www.yaskawa.de