Notre gamme de robots industriels à grande vitesse, à la pointe de la technologie, comprend des robots à forte capacité, à portée étendue, des robots 7 axes extrêmement agiles, ou encore des robots double bras à 15 axes.
Rohrbefestigungen Hammerschmid GmbH ventures into the future with Yaskawa Motoman robots
50 years of success due to flexibility – and automation
As a family-run business based in Marchtrenk (Upper Austria), Rohrbefestigungen Hammerschmid GmbH has successfully asserted itself on the international market. Besides the high qualification of its employees, this was also due to the consistent automation of individual processing steps. At the end of 2021 the company celebrated its 50th anniversary – and made itself a gift of two new Motoman welding robots.
Founded in 1971, some 50 years ago, as a classic metal construction company, Rohrbefestigungen Hammerschmid GmbH has become one of the leading international manufacturers for industrial and plant engineering. Customers in over 30 countries worldwide place their trust in the pipe clamps, carriages and hangers of this Upper Austrian family enterprise.
Combination of several success factors
Christian Hammerschmid Jun. and his sister Jacqueline Hammerschmid already represent the third generation. Both of them agree: “If we as a relatively small company can celebrate such an anniversary, we must have done a lot of things right”. The junior bosses name several reasons for this sustainable success: first of all, the outstandingly qualified workforce. With their many years of experience they enable the high product quality, as concentration on one product group – “rather a happy coincidence” – calls for a high degree of specialization. That is why engineering and production at Rohrbefestigungen Hammerschmid lie in one hand. Production takes place exclusively at the company headquarters in Marchtrenk – “and it will stay that way,” the grandchildren of the company founder insist.
Another decisive success factor is the extreme flexibility with which Rohrbefestigungen Hammerschmid reacts to current market demands. The core portfolio is constantly being supplemented by customized products and innovations such as the recently developed hygienic clamps for the food industry and cold-insulated pipe clamps in various designs. And last but not least, over the years those responsible have regularly increased the production capacities. This took place on the one hand by way of additional floor space and on the other by automation, primarily with the use of industrial robots.
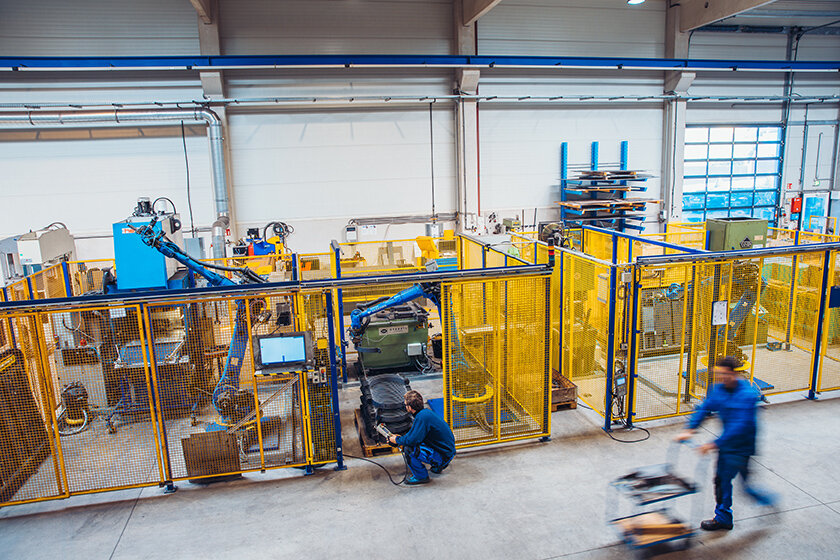
“A step into the future” with three handling robots
Christian Hammerschmid Jr. describes the characteristic setting: “We have neither single parts nor mass production.” As a rule, the number of parts manufactured by Rohrbefestigungen Hammerschmid is between 50 and 5,000. In this quantity range, automation is by no means a foregone conclusion. Nevertheless, in the course of new construction in 2015 the management of Rohrbefestigungen Hammerschmid decided to venture into robotics. As seen from today’s perspective it was “a step into the future”.
Now, three handling robots from Yaskawa’s Motoman MH series perform various different tasks: The models with payloads of 35 and 50 kg feed and unload the machines of a press configuration and are also used for palletizing. The main advantage lies in higher cycle counts. Work steps are implemented faster, and employees have more time for more demanding activities.
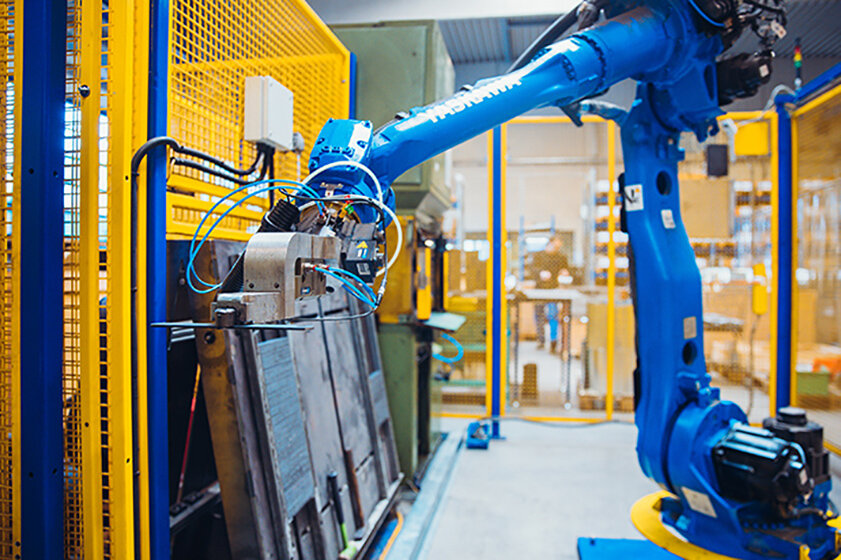
Robot-based welding as a second step
Based on this positive experience, in the anniversary year 2021 the decision was made to purchase two more robots for welding tasks: a Motoman AR900 for longitudinal and girth welding, and a complete ArcWorld CS welding cell featuring a Motoman AR2010 welding robot.
The precise 6-axis robots of Yaskawa’s current AR series were specially developed for the exacting requirements in the field of arc welding. Here they ensure particularly short process times, resulting in increased efficiency and energy savings. The AR900 is thus the ideal support for the welding head. The compact 6-axis robot also enables all-round welding of nuts, sleeves, rods and tubes. Executed in the high protection class IP67, it is optimally protected against weld spatter.
The ArcWorld CS robot welding cell has a small footprint and demonstrates a high level of flexibility: a Motoman AR2010 welding robot, positioner, control and power source are assembled on one platform. The robot cell can thus be moved quickly and easily if necessary. Because the cells are simple to install by the plug-and-play method, this is a cost-effective and uncomplicated way for smaller companies to get started in robot-based welding. With a payload of up to 12 kg and a maximum operating range of 2,010 mm the Motoman AR2010 integrated into the ArcWorld CS enables simple machining of workpieces that are bulky and difficult to access, at the same time ensuring high quality results.
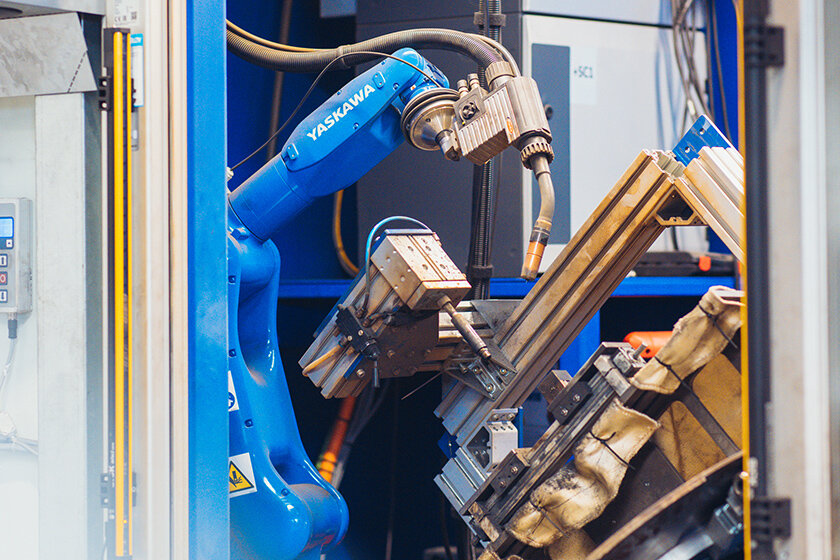
Summary and outlook
Following several years of experience with Yaskawa’s Motoman industrial robots, Christian Hammerschmid Jr. of Rohrbefestigungen Hammerschmid is convinced: “Automation is worthwhile, even at 50 pieces.” After an “initial acquaintance phase” everything was working smoothly. From the very beginning, the junior boss has programmed the robots. An additional new colleague is now being familiarized with the system.
Christian Hammerschmid Jr. also ventures a look into the future: “That’s certainly not yet the end of the flagpole.” In other words: the new welding robots will not have been the last robots in Marchtrenk. After all, at Rohrbefestigungen Hammerschmid they have further plans for the next 50 years.
Pictures: MecGreenie
Author and Contact for readers’ enquiries:
Sepp Hautzinger, Robotics Division (Sales Office Austria), Schwechat-Wien
Yaskawa Europe GmbH
Tel. +49-8166-90-0
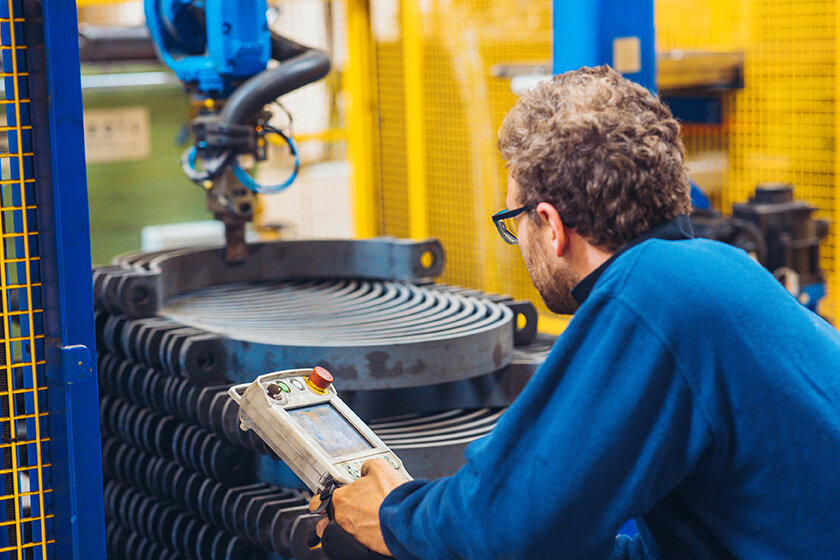