Plus de 100 ans d'engagement en faveur du progrès technique ont fait de Yaskawa le fabricant leader dans les domaines des variateurs, de la technologie d'entraînement et de la robotique.
GMG implements Yaskawa GP12 robot for container feeding in the labelling process of a pharmaceutical company
Thanks to Yaskawa's MOTOMAN GP12 robot, the labelling machine designed by GMG for a customer in the pharmaceutical sector is capable of labelling 40 containers per minute, in several different formats.
GMG, a company specialising in labelling machines, was faced with the challenge of optimising the container feeding process for a new drug developed by one of the leading companies in the pharmaceutical sector. The company was looking for an automated solution that would guarantee efficiency and precision in production, optimising the process to increase productivity.
With extensive experience in the manufacture of labelling machines, GMG developed a complete project that would solve all their needs. To bring this solution to fruition, they were faced with the need to integrate a robotisation system for container infeed into their production line.
Motoman GP12 for container feeding in the labelling process
GMG needed a machine capable of handling different tray formats accurately and efficiently at a high throughput rate. Specifically, the infeed process involved handling several tray formats, one for each type of container.
Fortunately, the customer already had a Yaskawa solution in place and, happy with the performance it was delivering, they wanted to continue to rely on the Japanese company for this new installation.
With their specific needs clearly defined, GMG contacted Yaskawa Ibérica. Yaskawa carried out a meticulous analysis of both the production process and the solution designed by them. In addition, they also carried out an exhaustive study and dozens of simulations of movements and time to see which was the best robot for this specific project. Once they had verified that it was capable of meeting the cycle times required by the customer, they came to the conclusion that the best option was the Motoman GP12 compact handling robot.
This easy-to-install and easy-to-maintain solution offers a payload capacity of up to 12 kg. In addition, its high operating speed and a reach of 1440 mm allowed it to comfortably meet the customer's handling and pacing requirements. Finally, its IP65/67 protection system and its certifications in terms of safety, ease of cleaning and hygiene, perfectly matched the needs of an industry such as the pharmaceutical industry.
A sector which, because of the role it plays in the well-being of society, requires any equipment that comes into contact with products to undergo a thorough documentation process ranging from certifications to materials used, validation of plans (electrical installation, programming, etc.), etc.
In the words of Xavi Muntal, General Manager of GMG: "It was very easy to work with Yaskawa. Regarding the programming of the robot, which is the most complex part, they sent a specialist who helped us with everything. This is something we will keep in mind for the future because our team already knows the robot, its specifications, the programming and integration are very easy and they offer great customer service.”
Specific design for particular needs
The project posed a number of interesting challenges for the company, beyond the quality and hygiene regulations. For example, the feeding of the containers, mentioned above, was perhaps the most complex in the design phase.
To solve this, GMG designed different grippers and programmed the repetition of movements for each format to take into account both the shape of the trays and the position of the injectables. In addition, the system has its own traceability thanks to a camera for viewing and positioning the label.
In addition, the customer also required the system to have a number of accumulations of several stacks of trays, which added an extra difficulty when programming. GMG designed a system in which, once the containers are fed, the empty trays are also stacked on an outfeed conveyor. In this way, when they reach a specific accumulation, they are removed with belts that free the operator from having to focus exclusively on this task. The result is a labeller with an autonomous working time of between 10 and 15 minutes, depending on the format.
Finally, as this is a very exclusive product for human consumption, its labelling had to be extremely precise, so a rejection system had to be integrated for all injectables that were not correctly qualified. Thus, when the solution marks the label with the batch number and expiry date, if the injectable does not meet a series of parameters, it rejects the label.
This was a process that prior to the installation of the GMG labeller was carried out manually, giving rise to potential human error. After automation, which required a second camera to verify the marking, not only has the process been speeded up, but the possibility of any kind of error has been eliminated.
40 containers labelled per minute, in various formats.
The end result is a fully automated labeller, capable of labelling up to 40 containers per minute, in various formats. In other words, capable of labelling 2,400 products in an hour.
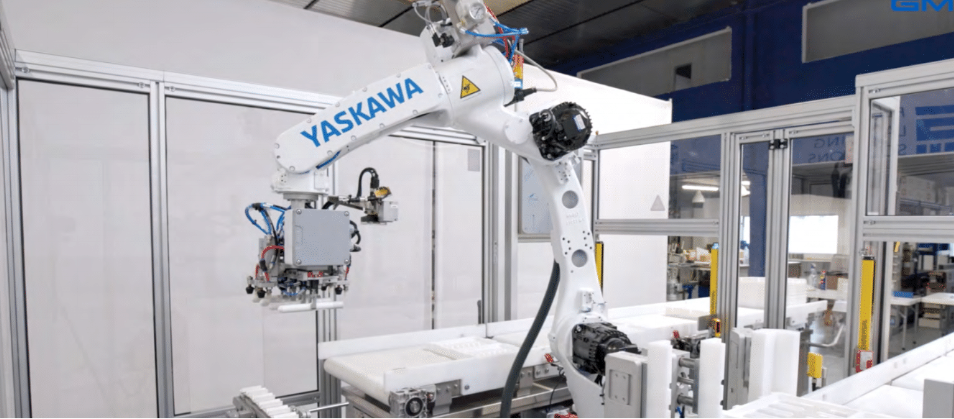